Maintenance is a very important aspect for organizations. Maintenance can impact the profit ratio of organizations. It is a major factor of good functioning production. Maintenance can help in controlling cost and if assets and equipment are not provided with proper maintenance then it can result in increased maintenance expenses. Furthermore, it can lead to sudden asset breakdown as well. But organizations utilize predictive maintenance for more effectiveness.
Now organizations want to minimize human effort & increase efficiency! How this can be achieved? With automation, predictive maintenance tools, and artificial intelligence!
What Is Predictive Maintenance?
Predictive maintenance is a type of proactive maintenance. With the help of , assets and equipment become more reliable and it helps in making the asset more efficient.
Basically, the predictive maintenance technique is designed to determine the condition of the equipment that helps in predicting when maintenance shall be done! This is why it is known as predictive maintenance.
This maintenance provides several benefits such as minimizing maintenance cost and sudden asset breakdown is decreased. Business suffers a lot due to sudden asset breakdown because it leads to production interruption and when products are not delivered to the customer then customer disappointment occurs and business loss occurs.
Sometimes people use the term preventive maintenance in the place of predictive maintenance but they have a difference which is predictive maintenance uses the resource to its full extent whereas preventive does not and this is why it is more powerful compared to preventive maintenance.
In predictive maintenance, assets are watched over regularly to see their performance, and data is collected. It helps in key performance indicators and condition monitoring. The end goal is to achieve efficiency and decrease maintenance expenses.
According to Statista, “It is expected that the global predictive maintenance market will reach around 23.5 billion U.S. dollars by 2024. The market is expected to grow at a compound annual growth rate of almost 40 percent between 2018 and 2024.”
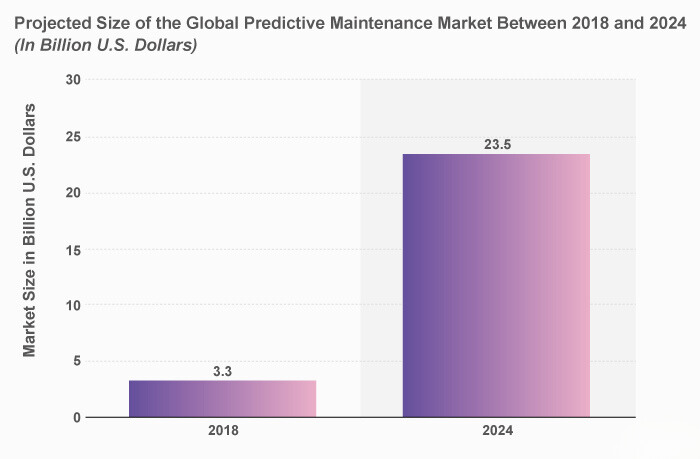
What Are the Main Predictive Maintenance Tools That Can Be Beneficial for Business?
Main predictive maintenance tools that can be beneficial for business are as follow:
1. Condition Monitoring
All assets have some issues; condition monitoring helps in identifying those issues as it can assist by revealing the exact reason for asset failure and when asset reliability increases it helps in business growth. Furthermore, condition monitoring can assist in predicting future anomalies. This tool can help in improving equipment dependability.
2. Maintenance Logs
When you have a lot of data you can filter, analyze the maintenance logs of each asset. However, you will need lots of equipment of the same or similar type. With the help of automated software, you are informed and make better decisions. Maintenance logs also assist in finding out which asset is taking more maintenance than required. Which type of activities are occurring in maintenance such as part replacement etc. With these types of records, you can know how long inventory (specific part) works once it is installed.
3. Data Reports
One of the most important tools used in predictive maintenance is reports based on data. These reports contain crucial information and details that are helpful in understanding the asset and predict asset performance, breakdown, etc.
With the help of the predictive maintenance reports tool, you will notice decreased maintenance iteration furthermore their maintenance work is also reduced. As a result, overall downtime is decreased and asset performance will increase as well.
4. Asset Meter Reading
here are some types of equipment that need to break at regular intervals or after a certain time, it starts to heat. Many assets come to maintenance for this reason only. Sometimes it is hard to keep track of how long equipment is working thus this with this preventive maintenance software tool you get alert and you can stop the machine and avoid breakdown.
What Are the Advantages of Predictive Maintenance?
The advantages of predictive maintenance are as follow:
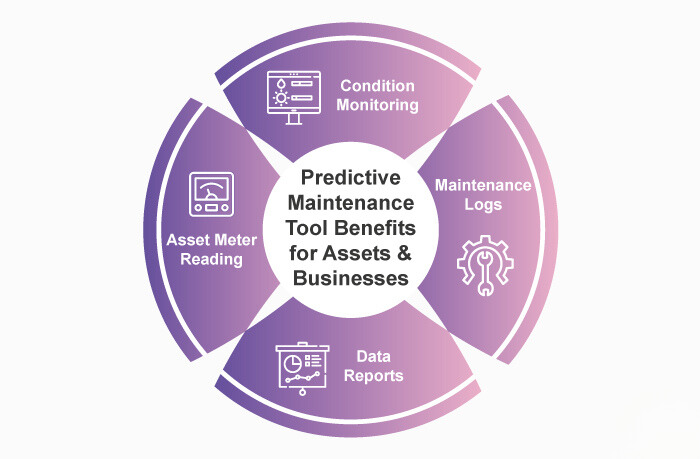
1. Decreasing Downtime
The Downtime of assets is a big issue for organizations. Downtime is a state in which assets are not working, either it can be for maintenance purpose or due to breakdown, etc. The downtime can be planned or unplanned.
But with predictive maintenance, you can reduce the meantime to repair (MTTR). How? As we know predictive monitoring is continuous monitoring & analysis of assets, you can identify the faulty areas of assets and improve them accordingly.
2. Sudden Asset Failure
Sudden asset failure occurs due to negligence of maintenance or mismanagement of assets. Overall, mostly it happens due to human error and miscalculations. You can easily avoid asset failure or repair those part which is not working efficiently with the help of predictive maintenance.
Furthermore, it has the capability to estimate the mean time between failures (MTBF). When asset breakdown is decreased then the maintenance team can utilize their time in other tasks.
3. Proactive Maintenance
Assets are provided maintenance at the right time which means before any incident or asset failure can occur. Each asset is scheduled for maintenance.
As a result, sudden asset failure chances are minimized, downtime decreases and the maintenance team can focus on calibration management. The benefits of predictive maintenance do not end here it also helps in minimizing maintenance expenses and inventory expenses.
4. Increasing Performance
Performance stabilizing is very important because equipment runs continuously for several hours and this is where asset performance starts decreasing.
That is why maintenance is important to give on time. The regular monitorization of assets helps in predicting when assets require maintenance.
Conclusion
There is no doubt that data-driven technology is the future of maintenance. Predictive maintenance tools help in increasing the efficiency of the business and make assets more reliable.
If you want to stay ahead of your competitors then it is high time to take initiative and invest in Helpdesk Management Software that can help in making the data-driven decision and not just based on assumptions.
Frequently Asked Questions (FAQs)
1. What are the benefits of predictive maintenance tools?
These tools provide real-time information & they provide accurate information. Furthermore, they give a signal of how assets are performing after maintenance. These predictive maintenance tools monitor asset health continuously, generate and analyze data in order to deliver accurate information.
2. What are the advantages of predictive maintenance?
Disadvantages of Predictive maintenance are as follow:
1. Need Proper & Accurate Planning.
2. Time-consuming Process.
3. Spare Parts are required.
4. Resources can be wasted.
3. What is Planned and Unplanned Downtime?
Planned downtime is when the maintenance team plan scheduling of asset maintenance for boosting performance or regular maintenance. Unplanned downtime is just the opposite it is not scheduled or planned; Sudden failure of assets leads to an unplanned schedule. Downtime will automatically decrease when assets are maintained, performing at their best level.