CMMS is essential for keeping track of work order, inventory purchasing requirements, and their status as well. The computerized maintenance management system is built to keep machines and equipment in top condition and well maintained. It is helpful in maintenance tracking and maintenance budgeting.
What Is CMMS?
Computerized maintenance management system, in short CMMS. It is helpful in scheduling maintenance of assets. CMMS software is an effective tool for keeping track of maintenance.
It can update you about each maintenance work order. For example, how much work is done! And how many tasks are left, which technician is working on the work order, and when it will be completed!
It eliminates the manual process of tracking maintenance. We know the manual process is prone to error especially when an organization is equipped with a lot of assets. Now managers do not have to keep track of maintenance because CMMS does it for them. It also keeps the manager free to focus on other activities.
One of the main aims of CMMS is to avoid sudden asset breakdown. Sudden asset breakdown can be harmful to the organization's bottom line. In the same way, it avoids over maintenance of machines and equipment. Therefore, the CMMS system increases the productivity of the organization and saves maintenance expenses.
How CMMS Can Help in Maintenance Budgeting?
There are lots of organizations that make a business decision on just assumption and guesswork. They do not have concrete numbers or no actual data on what work was done in the last few days or what is the plan for the future. Similarly, budgeting maintenance is also done on assumption.
Now CMMS assists the organization in many ways as they keep track of not only maintenance but also how much expenses are done in maintenance including maintenance expenses as well. Since CMMS keeps track of maintenance history, managers can use the data and can use it for maintenance budgeting.
Managers can plan how much budget they should keep for planned maintenance and emergency maintenance! How much scheduling maintenance activity shall be done (weekly, monthly, quarterly, or half-yearly)! It is easy to calculate since it is a planned activity.
On the other hand, an emergency maintenance budget is not simple because it is unpredictable and cannot say what activities need to be performed because technicians are not aware of inventory, they need to bring the asset into running condition.
However, CMMS has all the information and asset history that will help calculate the average maintenance cost.
If any asset is taking more maintenance than required then you can know it with the CMMS software. You can sell this particular asset & replace it with an updated version of the asset. Similarly, you can know when asset useful and productive life is about to end.
How CMMS Can Help in Maintenance Tracking?
Maintenance tracking is very important for an organization as it can impact ROI (Return on Investment). Over-maintenance is an issue as well as not providing enough maintenance is an issue for equipment and organizations as well. Maintenance shall be neither too much nor too little. Therefore, maintenance tracking is crucial.
When maintenance tracking is also significant because it can increase or decrease the performance of the asset. For the best performance of equipment and machine, maintenance shall be done at regular intervals. It boosts asset performance.
CMMS software provides equipment maintenance history which is helpful in maintenance tracking. CMMS software alerts you in for equipment maintenance.
Incase maintenance tracking is not done it can result in:
- Asset breakdown
- Downtime increase
- Decrease asset life
- High maintenance expenses
- Frequent machine malfunctioning
What Are the Benefits of CMMS?
According to Statista, “The advantages of adopting computerized maintenance management systems (CMMS) in the manufacturing industry worldwide in 2017. As of that time, 65 percent of the respondents indicated that CMMS helps improve the overall efficiency of plant manufacturing.”
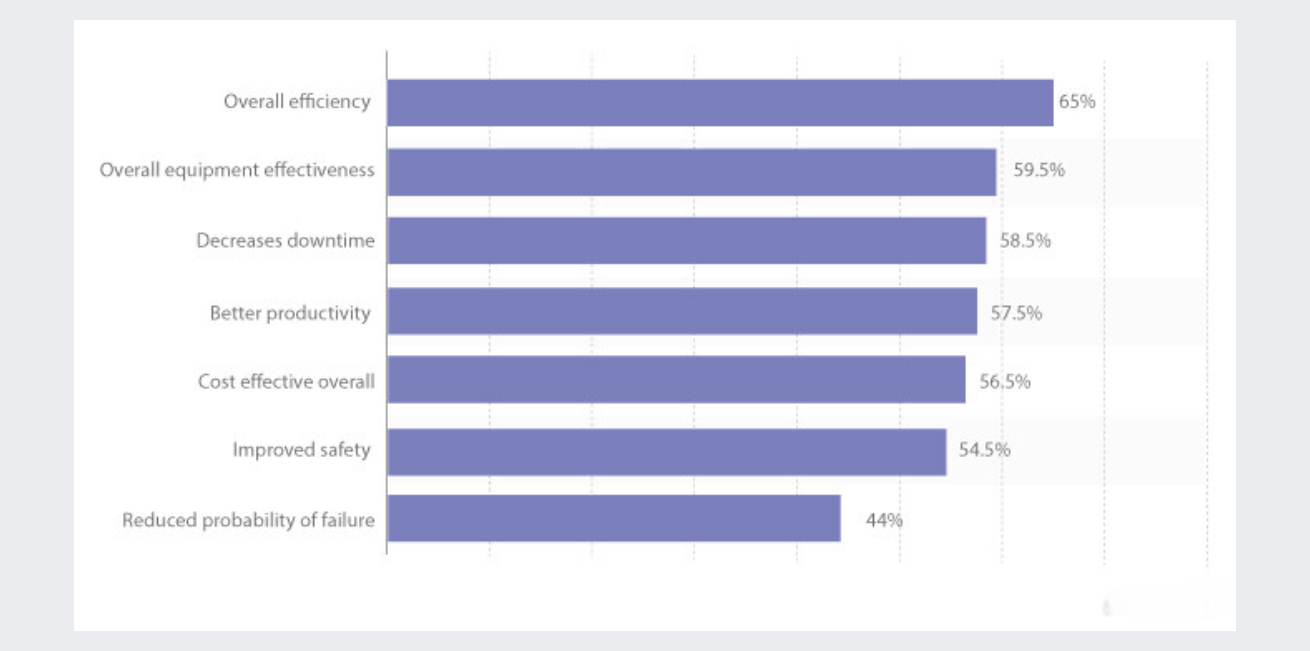
CMMS is very useful for all industries, especially those organizations which have several assets. Those organizations also, for which maintenance is very crucial! Here are the benefits of CMMS:
- Track maintenance - With CMMS software you can easily keep track of maintenance.
- Simple maintenance scheduling - CMMS provides assets details about maintenance too. You can schedule maintenance. CMMS can also remind us about maintenance.
- Optimize equipment performance - If maintenance is given on time then asset efficiency & productivity is also enhanced.
- Decrease equipment downtime - Maintenance given on time decreases equipment failure chances.
- Increase equipment lifespan - Another benefit of maintenance given on time that it can increase asset life.
- Calibration management - Calibration management is done to enhance the efficiency of the equipment. It is like servicing equipment to add a new feature.
- Maintenance cost saving - Emergency maintenance is more expensive compared to planned maintenance. CMMS provides stability in maintenance so maintenance expenses are minimized.
- Maintenance budgeting - Budget
- Work & purchase order tracking - CMMS keeps track of each work order as well as a purchase order.
- Safety regulatory compliance - Some rules need to be followed as per the government regulations. This is done for employee safety purposes.
- Effective maintenance audit process - An audit with CMMS can uncover actual issues with the maintenance system. CMMS can assist in what needs to be done to enhance performance.
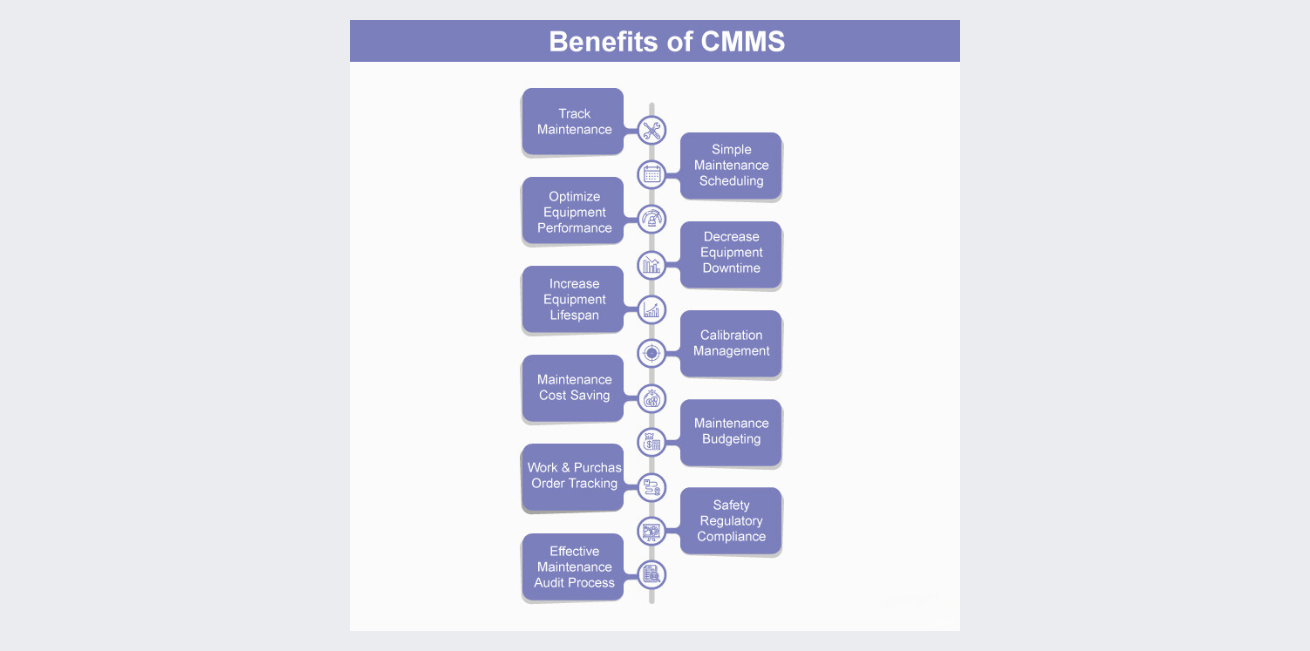
Conclusion
A computerized maintenance management system can be very beneficial for an organization. CMMS helps in accomplishing your goal. The real value of the asset does not lie in its features or price but in the utility of the asset.
CMMS assists in revealing flaws and boosting performance and life. Hence, you must invest in a computerized maintenance management system for company growth.
Frequently Asked Question (FAQs)
How CMMS is different from asset management software?
CMMS is mainly focused on maintenance tracking whereas asset management software focused on asset management including maintenance tracking. In short, asset management software has more features including CMMS features as well.
Name the top 5 industries for which CMMS software will be effective?
1. Manufacturing industry
2. Construction industry
3. Oil and gas industry
4. Fleet industry
5. Servicing industry
CMMS will be effective for these above-mentioned industries.
How much CMMS software cost?
CMMS is available on a monthly or yearly subscription basis and also could be per user per month or location per month. The charges completely depend upon various factors, like the number of assets, features, users, or location that you want to manage. You can try a 14-day free trial with our CMMS.